PP meeting is a very important part of Garments manufacturing process, a part of the pre-production process to be completed in the right time for smooth Garments manufacturing process.
PP Meeting Requirements and Procedure in Apparel Industry
A process where buyer QC/Merchandiser are also involve in checking accuracy. Generally, PP meetings conducted by buyer QC, internal PP meeting by garments manufacturer before that, is a good practice to avoid the risk of failing, meeting location factory conference room, or inspection room.
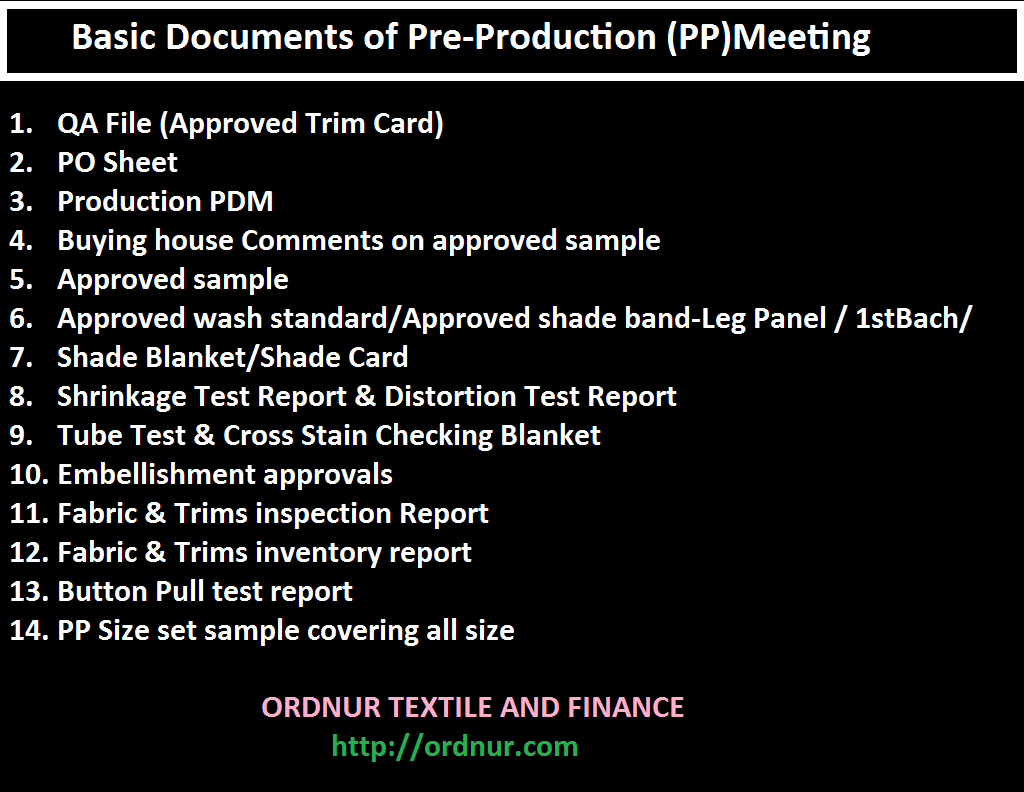
Basic Documents of PP Meeting
- QA File (Approved Trim Card)
- PO Sheet
- Production PDM
- Buying house Comments on approved sample
- Approved sample
- Approved wash standard/Approved shade band-Leg Panel / 1stBach
- Shade Blanket/Shade Card
- Shrinkage Test Report & Distortion Test Report
- Tube Test & Cross Stain Checking Blanket
- Embellishment approvals
- Fabric & Trim’s Inspection Report
- Fabric & Trims inventory report
- Button Pull test report
- PP Size set sample covering all size
You may love to read
Factory Quality Team Responsibility before PP Meeting
- Assigned Quality controller receives all
approvals and records them on “PP
Meeting checklist”. QA also records expected date of receiving non-available
approvals and follows up accordingly with Production merchandiser. - The QA marks “NA” (not applicable) in case of
anything not being used for the particular style. - Need to do internal PP meeting by factory QA
manager with his QC and production before submitting sample for buyer QC PP
meeting.
PP Meeting Activities
Fabrication & Finish Issues
- All
expected fabrication issues especially those highlighted by during fabric
inspection report & sample process. - Potential
production problems according to fabric behavior. - Fabric
quality, CSV/SSV, Shrinkage, Shade, Cross staining & Wash issues.
Cutting Issues
- All cutting related issues to be highlighted –fabric
relaxation, spreading elongation and tension, panel checking and records
measurements variation, plaid matching, pattern adjustment etc. - Grading of pocket, panels, inserts, notches etc.
Embellishment Issues
All potential issues in application of embellishment i.e. print, embroidery, rhinestone, heat transfer label, decorative patches etc. are discussed.
Construction and Stitching Issues
- Sample
comments regarding sewing issues and every operation of concerned style is
discussed. - Emphasis
is on critical operations. All out of routine operations are discussed with
sampling master which finalized in vendor pre-production meeting. - Difficult
operations are highlighted and displayed for every style and doing risk
analysis report. - Difficult
operations checklist is maintained and verified during production.
Finishing Issues
- All
expected finishing and packing issues to be highlighted & discussed with
vendor. This includes garment shape, pressing, folding, packing etc. - Pressing,
measuring, QA check, folding & packing instructions are placed and clearly
demonstrated to ensure PDM instructions are properly followed. - Factory
specs men are advised how to measure before pressing & after pressing &
keep records. - Buyer QC
emphasizes on vendor pre-production meeting points during inline inspections. - Factory
merchandiser gives production time and action plan (T.N.A) to buyer QC in pre-production meeting. - After
conducting pre-production meeting, buyer QC distributes pre-production meeting
recap/Comments to all participants through e mail or hard copy.
PP Meeting Participants
- Head of operation
- Production Manager (PM)
- Operation & Production in charge
- Technical Manager, Sampling QA and Pattern master
- Production merchandiser
- QA Manager
- GPQ
- Fabric, Store & Finish Manager
- Cutting, Sew & Finishing Manager
- Maintenance & IE Manager
Please send me garment ppm comments format [email protected]
good helpful for me