A Successful Implementation of Lean Manufacturing in Garments Factory Works as a Driving Force to Ensure Effectiveness in Operation
What is Lean Manufacturing?
Lean manufacturing is a systematic methodology to eliminate waste (non-value-added activities) by continuous improvement which adds value to the customer and surely in manufacturing as well but without hampering productivity. Lean Manufacturing is all about optimizing processes, eliminating waste; eliminating inventory, building a quality product, a more efficient workplace with less cost, and human effort. The manufacturing system is work for customer satisfaction and optimization of all resources.
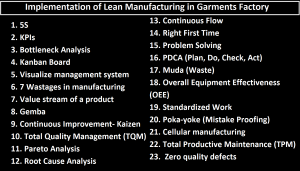
Benefits of Lean Manufacturing
The benefits and advantages of lean manufacturing will be more clear to you after reading this below mention list:
- Improve productivity and quality
- Reducing Work in Process (WIP) inventory.
- Eliminate waste and problems
- Reducing inventory area
- Reduce cycle and lead time
- Production flow and controlled automation
- Reduce manpower, time and space
- Improve visual management
- Reducing machine downtime
- Optimize resources
- Sustainability, employee satisfaction, and increase profit
- Improve workplace and organize.
- Improve safety conditions and housekeeping.
- Increase customer satisfaction and customer service
Principles of Lean Manufacturing
5 principles of lean manufacturing can be applied in any manufacturing industry.
- Define Value
- Map the Value Stream
- Create Flow
- Establish Pull
- Pursue Perfection
Lean Manufacturing Tools Used in Garments Industry
- 5S
- KPIs
- Bottleneck Analysis
- Kanban Board
- Visualize management system
- 7 Wastages in manufacturing
- Value stream of a product
- Gemba
- Continuous Improvement- Kaizen
- Total Quality Management (TQM)
- Pareto Analysis
- Root Cause Analysis
- Continuous Flow
- Right First Time
- A3 Problem Solving
- PDCA (Plan, Do, Check, Act)
- Muda (Waste)
- Overall Equipment Effectiveness (OEE)
- Standardized Work
- Poka-yoke (Mistake Proofing)
- Cellular manufacturing
- Total Productive Maintenance (TPM)
- Zero quality defects
5S
5S is the first step to implement lean manufacturing, it helps to keep workplace organize and clean. It is actually
We have two articles on 5S you may love to read
KPIs
Key Performance Indicator (KPI) is a performance measuring tool which helps to know about a company the situation of their achieving goals and data of their performance.
You may love to read this detail article: KPI Factors of Garments
Bottleneck analysis
Kanban Board
Kanban is visual display board for visualizing to do list, command what to do to reduce overproduction in the manufacturing floor.
Please read this article to know more about it. Kanban Board in Garments Manufacturing Production Floor
Visualize Management
Visual management need for an organization that provides information for everybody who can analyze large amounts of data and produce reports that provide meaningful value. Visualization could become the remedy for generating actionable information for the apparel industry.
Please read this article to know more about it. Visual Management System in the Apparel Industry
7 Wastages
Waste is the use of resources over and above what is actually required to produce the product as defined by the customer. Lean manufacturing reduce 7 wastages in types of manufacturing, 7 wastages (Mudas) are:
- Transport
- Inventory
- Motion
- Waiting
- Over-Processing
- Overproduction
- Defects
Value Stream of a Product
Value stream mapping is a lean manufacturing or lean enterprise technique used to document, analyze and improve the flow of information or materials required to produce a product or service for a customer.
Gemba
Gemba is Japanese terms which mean to go actual problem occurring place, ask and collecting information from a real place rather than just sitting in the office and depending on other people to collect data.
Continuous Improvement
Continuous Improvement is a philosophy of never-ending improvement. Continuous improvement is an ongoing effort to improve products, services or processes. These efforts can seek “incremental” improvement over time or “breakthrough” improvement all at once.Read more from Continuous improvement
Please read this article to know details about it Implementation of 7 QC tools in the apparel industry
Total Quality Management (TQM)
Total quality management is the management approach of an organization, centered on quality, based on the participation of its entire membership and aiming at long term success through customer satisfaction. TQM is long time oriented teamwork that requires leadership of top management and continuous involvement.
Philosophy of TQM
Customer focus | A goal is to identify and meet customer needs |
Continuous improvement | A Philosophy of never-ending improvement |
Employee empowerment | Employees are expected to seek out, identify and correct quality problems |
Use of quality tools | Ongoing employee training in the use of quality tools |
Product design | A product needs to be designed to meet customer expectations. |
Process management | Quality should be built into the process; the source of quality problems should be identified and corrected. |
Managing supplier quality | Quality concepts must extend to a company’s suppliers |
Pareto Analysis
Pareto Analysis named after the Italian economist, Vilfredo Pareto. The original observation was in connection with population and wealth. Pareto analysis is also known as 80/20 rule. Vilfredo Pareto observed that 80% of Italy’s land (Asset) was owned by 20% of the people. In the late 1940s, Dr. Joseph M. Juran, a Quality Management pioneer, applied this 80/20 Rule to quality control, calling it Pareto’s Principle. Pareto analysis is very much helpful for reducing garments defects that indicate 80% problem happen for 20% causes.
Root Cause Analysis
Root cause analysis is a problem-solving tool, works by identifying by problems, used by employees of manufacturing and work to solve. Root cause analysis is the best way to solve garments defects.
You may love to read this
Reducing sewing defects through root cause analysis
Continuous Flow
Continuous flow means running, moving or producing product continuously of every piece from raw material to finished product, not batch-wise production, called “1-piece flow”.
Right First Time (RFT)
RFT is quality improvement tools, very much important apparel industry; every section has a target to achieve certain RFT level.
Please read this article to know details about it RFT factors and calculation in Garments industry
A3 Problem Solving
A3 is a problem-solving tool, a challenge is to write explanation and solution in one page.The purpose of A3 tools is to analysis problem with root cause and define a direct solution.
PDCA
PDCA is plan-do-check-act or plan-do-check-adjust, 4 step management method for quality controlling and continuous improvement.
Overall Equipment Effectiveness (OEE)
Overall Equipment Effectiveness (OEE) means everything is productive in the manufacturing industry. OEE 100% mean manufacturing factory is fully productive, produce only good parts, no idle process, on the machine or other downtimes. If your factory OEE is 50%, surely their lots of things you have to improve and huge opportunity to develop.
Standardized Work
Standardized work is the most powerful lean tools by documenting the current best practice, the baseline for kaizen or continuous improvement. As the standard is improved, the new standard becomes the baseline for further improvements, and so on. Improving standardized work is a never-ending process.
Standardized work consists of three elements:
- Takt time, which is the rate at which products must be made in a process to meet customer demand.
- The precise work sequence in which an operator performs tasks within takt time.
- The standard inventory, including units in machines, required to keep the process operating smoothly.
You may love to read this Standardization of Apparel Manufacturing Industry
Poka-yoke (Mistake Proofing)
Poka-yoke is mistake-proofing tools which help to eliminate mistake in manufacturing floor, a quality control technique.
Cellular Manufacturing
Cellular manufacturing is manufacturing same types of product in cell which improve productivity and quality.
Total Productive Maintenance (TPM)
Total productive maintenance (TPM) is developed in 1960 based on 5S for effective machine and equipment to maximize operational efficiency increment.
Zero Quality Defects
Zero quality defects are the process of maintaining zero defects production through 100% inspection.
Lean Six Sigma certification courses
There are many institutions around the world that have Lean Six Sigma certification courses also available online courses to learn Lean Sigma and getting a certificate.
This content also refers below point’s information
- Application of lean manufacturing tools in the apparel industry
- Lean Manufacturing Techniques for garments
- Importance of lean manufacturing in the apparel industry
- Lean management in a garments factory
- 5 Principles of lean manufacturing
- Importance of lean manufacturing
- Lean process improvement in Garments
- List of lean manufacturing tools
- The lean management system in the apparel industry
- Lean concepts for garments manufacturing
- Lean production in Garments manufacturing
- Lean for garments manufacturers
- Continuous quality improvement in the apparel industry
- Application of Kaizen in Garments
Related articles you may love to read
- WIP calculation and reduction process’s in the Apparel industry
- Job responsibilities of Garments IE department
- Duties and responsibilities of an Industrial engineer in the apparel industry
- Productivity Improvement Techniques in Apparel Manufacturing Industry
- Technical Audit in the apparel industry
- Garments quality SOP
WELL UNDERSTOOD
Lean manufacturing plays a important role in garments manufacturing now a days ..as cost of production need to maintained and meet customer requirements …