A fabric rejection standard operating procedure (SOP) is a set of guidelines that outlines the steps that should consider when rejecting fabric due to quality issues. The goal of a fabric rejection SOP is to ensure that defective fabric is identified and separated from good fabric in a consistent and efficient manner, to prevent problems downstream in the manufacturing process.
Fabric Rejection Standard Operating Procedure (SOP)
The fabric rejection SOP must include the following thing to standardize the operation at the industrial level.
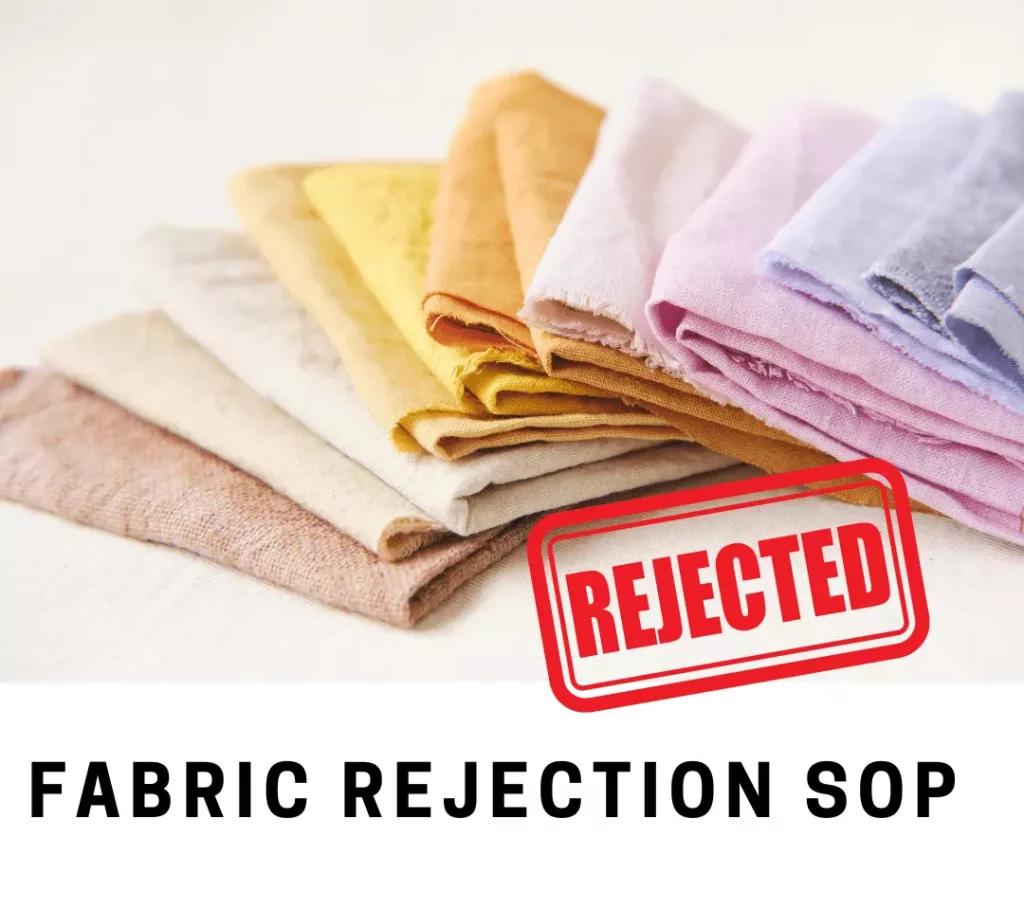
Identify the Problem
The first step in the fabric rejection process is to identify the specific issue with the fabric. This might include visual defects such as holes, stains, or shrinkage, or it could be issued with the fabric’s properties (e.g., strength, drape, or colorfastness). The person identifying the problem should carefully examine the fabric and record the location and nature of the issue.
Document the Issue
It’s important to thoroughly document the problem with the fabric, including the location and nature of the issue, as well as any other relevant information (e.g., the batch number or supplier of the fabric). This information will be needed for later investigation and for informing the fabric supplier of the problem. Separate the Defective Fabric
Once the problem with the fabric has been identified, the defective fabric should be separated from the good fabric. This might involve cutting the defective fabric into small pieces or separating it into a separate bin or container.
Notify the Appropriate Parties
The next step is to inform the fabric supplier, quality control team, and any other relevant parties of the problem. This might involve sending a notification email or filling out a defect report form.
Determine the Cause of the Issue
It’s important to investigate the root cause of the problem to prevent it from occurring again in the future. This might involve working with the fabric supplier to identify the cause of the issue, or conducting in-house testing to determine the cause.
Make a Decision About the Fabric
Once the cause of the problem has been identified, a decision must be made about what to do with the defective fabric. If the fabric can be repaired, it might be possible to fix the issue and use the fabric. If the fabric cannot be repaired, it will need to be rejected.
Dispose of the Fabric
If the fabric is rejected, it should be properly disposed of to prevent it from being used in the manufacturing process. This might involve sending the fabric back to the supplier or disposing of it in an appropriate manner (e.g., recycling or proper disposal).
It’s important to have a clear and thorough fabric rejection SOP in place to ensure that defective fabric is identified and dealt with in a consistent manner. This can help prevent quality issues and improve the efficiency of the garment manufacturing process.
Steps of Fabric Rejection
Here are a few steps you can follow to reject a fabric:
- Inspect the fabric: Carefully examine the fabric to identify any defects or issues that may make it unsuitable for use. This could include flaws in the fabric itself, such as holes, runs, discolorations, or issues with the way the fabric was cut or sewn.
- Keep Documents: Make a note of any issues you find with the fabric, as well as any relevant details such as the location of the defect or the severity of the issue. It may also be helpful to take photos or videos to document the issues.
- Notify the supplier: Contact the supplier or manufacturer of the fabric to inform them of the issues you have found. Be specific about the issues you have identified and provide any documentation you have to support your claim.
- Request a replacement: Depending on the severity of the issues, you may be able to request a replacement fabric or a credit for the defective fabric. It is important to work with the supplier to find a solution that is satisfactory to both parties.
- Return the defective fabric: If the issues cannot be resolved, you may need to return the defective fabric to the supplier. Be sure to follow any necessary shipping and handling guidelines to ensure the fabric is returned safely.
Rejecting a fabric can be a complex process, and it is important to follow the correct steps to ensure that the issue is handled properly. By carefully inspecting the fabric, documenting any issues, and working with the supplier to find a solution, you can ensure that your business only uses high-quality fabrics.