Cutting Section Standard Operating Procedure in Garments Industry
Cutting Section Standard Operating Procedure (SOP) is developed to provide guidelines for the workers so that they have proper knowledge of working. SOP is written in the simplest way to ensure a better understanding of all people who are involved directly or indirectly with those particular activities. In a garments industry, you may find different forms of SOP and it can vary company to company and also department to department.
Cutting Section SOP
Each and every garment company always try to make the best adaptable standard operating procedure. You know that cutting section is a very crucial part of garments manufacturing, keep in mind the importance of this section I made a simple Standard Operating Procedure (SOP) for cutting a section of garments so that can make SOP for your company. Now a day’s it is mandatory to make SOP and hang it to the working place of each section in the apparel industry for a better understanding of the procedure and to minimize operational error.
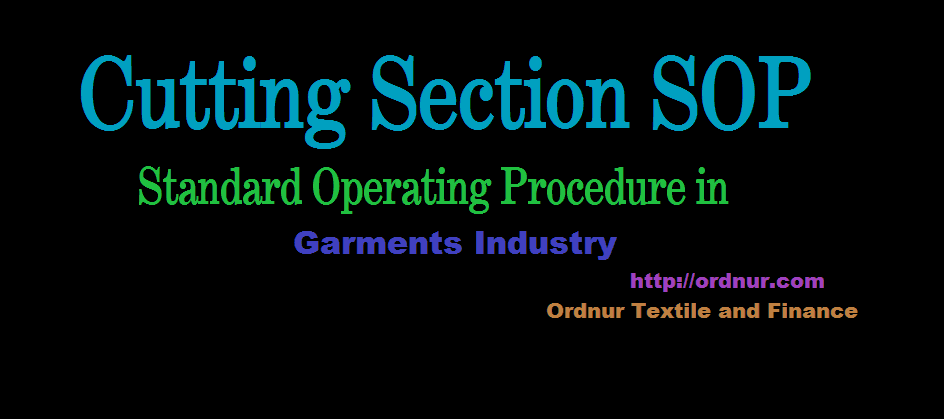
Sample form of Cutting Section Standard Operating Procedure is as flows:
Fabrics Relaxation Procedure
- Spandex fabrics will be relaxed a minimum of 24 hours making unroll in the cutting section.
- Relaxation date and time must be recorded. After spreading, will relax 2 hours before the cut.
Before Cutting Procedure
- Receive marker and quality check by cutting QC.
- Fabric Spreading will be done based on Shade chart/Shade grouping provided by the fabric warehouse.
- Spreading report will be made after spreading with related all necessary data.
- Spreading Quality checkpoint: -Table marking -Ends -Leaning –Tension -Narrow Goods -Remnants -Counts -Ply High -Marker Placing -Fabric Flaws
- The highest lay for woven fabrics is length 14 meters and height 3 inches.
- The Lay chart should be maintaining roll wise.
- The quality inspector will control quality inspection during fabrics lay.
- Cutting spreader man will spread marker after finishing lay.
- For stripe and check fabrics, alignment to be correct by using a hook, thread.
- Before cutting cutter man will attach clamp, Gum tap on the layer.
- Shade chart will be hanged during lay.
- Cutting Quality checkpoints: -Miss cut –Rugged Cutting –Notches-Matching Plies and pattern check.
After Cutting Procedure
- Quality will check every bundle using hard pattern three different positions of the bundle.
- Numbering and bundling separation done by following spreading report and identify each bundle by style, Cutting number, Bundle number, size, Serial number, Shade number, and Parts name.
- 100% cut panel will be inspected
- If any defective panel found, will be replaced from lay chart wise remnants by following shade and pattern grain line.
- The light color bundle will bind with a light color string; deep color bundle will bind with deep color string
- Light color Fabrics will be covered by poly in rack or pallet.
- Then all cut panels will be ready to deliver in sewing.
You can download cutting section SOP in Garment Industry from here.
Cutting Standard Operating Procedure SOP English
Cutting Standard Operating Procedure SOP Bangla
In a dress pant/formal pant project to get 6000 pcs cutting how many man power required.
it is the best policy for gmts quality standart.
nice post good info
Hello Dear team leader,
how are you?
Amy here from XinWu, a trusted Chinese textile papers&poly manufacturer by end users around the world, wants to pitch you with our products&services for your CAD/CAM cutting department.
We can provide all textile papers(perforated kraft paper, marker paper, plotter paper, newsprint paper, pattern paper board, underlay paper, interleaving tissue paper, newsprint paper…) and HD Poly overlay plastic film rolls.
If you and your team are interested in our products&services,
do not hesitate to contact me at any time!
We as the direct factory manufacturer, can provide you
1/ No MOQ requirements, you can always purchase the quantity exactly needs;
2/Factory directly economical&the best rates for you, you will save more production costs;
3/Factory stable&strong quality approved by all end users who purchase from us all the time;
4/Quick manufacturing and leading time all the time.
5/Free samples developing for you testing all the time.
….More benefits and services can be discovered if we cooperate in the near future.
Thanks for your time,
Best regards| Amy Tan
import&export department|Dongguan Xinwu Trade CO.,LTD
Mobile/Whatsapp: +86 1352 8655 634
Wechat ID: xwamy2020
V good effort ,now we need some easy method to do better
My question is
When we do cutting inline.please answer the good keys
we want knits fabric (single jersy,pique,fleece ) layer height as per interntional market quality standard.