This article is about very basic of lean manufacturing, definition, principle, importance, and steps how you take initiatives to introduce to lean manufacturing in your garments manufacturing industry. Hope this writing would help you to get an idea of Lean Manufacturing initiatives.
Lean Manufacturing Initiatives in Apparel Industry
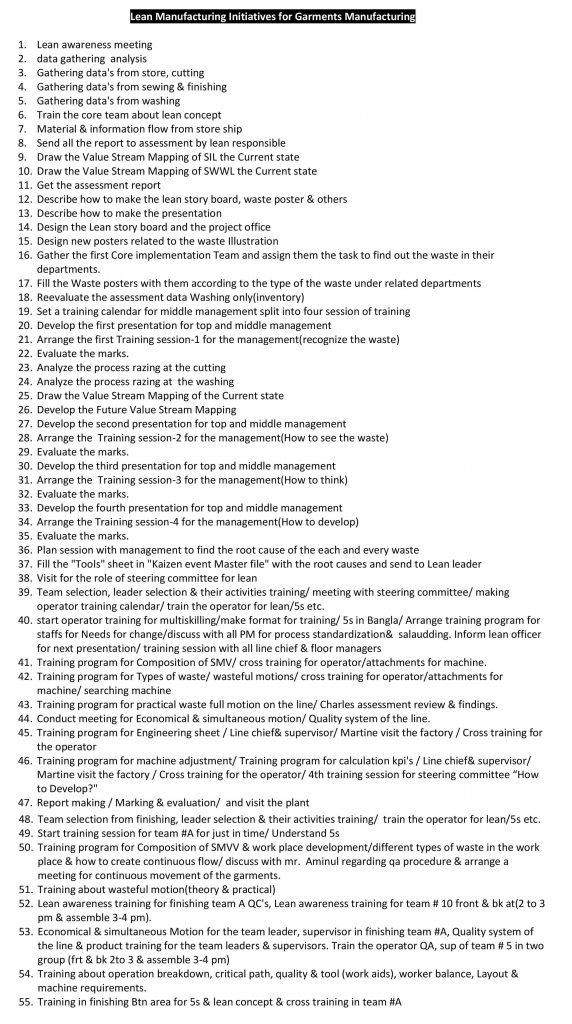
What is Lean?
A lean is a way of maximization of the benefit by ensuring proper utilization of resources without increasing its cost or wasting any materials. This is a systematic approach to minimizing the cost of any process that can be applicable for production or service-oriented companies. Lean manufacturing is nowadays commonly used the term in the apparel industry. The main objective is to reduce the production cost of garments. Although all companies using a systematic approach of lean manufacturing to reduce the wastage and maximize productivity but they do not name as a lean. Finally, we can say lean is a tool that uses a systematic approach to minimize the production cost which ultimately increases the productivity and overall profit of the company.
Principles of Lean Manufacturing
- Recognition of waste
- Standard the process
- Continuous flow
- Pull production
- Quality at source
- Continuous improvements
- Value-define by the customer
- Perfection
Why Lean is Important for the Company?
- It helps to eliminate the waste
- Makes a better environment at home & office.
- Change the culture
- Better understanding
- Productivity improvement
- Better quality
- To take the challenge of future business
Steps of Lean Manufacturing
- Value stream mapping
- Kaizen- continuous development
- Workplace organization-5s
- Quick change over- small quantity
- Overall equipment effectiveness- maximum utilization of people instead of mc
- Pull production
- Kanban– instruction card
- Six Sigma- statistical method of systemic analysis to reduce process variation use damic.
- Total productive maintenance- all level of function to maximize OEE
- Cellular manufacturing
Keys to Lean Success
- Prepare & motivate people
- Employee involvement
- Identify & empower champions
- Atmosphere of experiments
Lean Manufacturing Initiatives for Garments Manufacturing
- Lean awareness meeting
- data gathering analysis
- Gathering data’s from the store, cutting
- Gathering data’s from sewing & finishing
- Gathering data’s from washing
- Train the core team about the lean concept
- Material & information flow from storeship
- Send all the report to assessment by lean responsible
- Draw the Value Stream Mapping of SIL the Current state
- Draw the Value Stream Mapping of SWWL the Current state
- Get the assessment report
- Describe how to make the lean storyboard, waste poster & others
- Describe how to make the presentation
- Design the Lean storyboard and the project office
- Design new posters related to the waste Illustration
- Gather the first Core implementation Team and assign them the task to find out the waste in their departments.
- Fill the Waste posters with them according to the type of waste under related departments
- Reevaluate the assessment data Washing only(inventory)
- Set a training calendar for middle management split into four sessions of training
- Develop the first presentation for top and middle management
- Arrange the first Training session-1 for the management(recognize the waste)
- Evaluate the marks.
- Analyze the process razing at the cutting
- Analyze the process razing at the washing
- Draw the Value Stream Mapping of the Current state
- Develop the Future Value Stream Mapping
- Develop the second presentation for top and middle management
- Arrange the Training session-2 for the management(How to see the waste)
- Evaluate the marks.
- Develop the third presentation for top and middle management
- Arrange the Training session-3 for the management(How to think)
- Evaluate the marks.
- Develop the fourth presentation for top and middle management
- Arrange the Training session-4 for the management(How to develop)
- Evaluate the marks.
- Plan session with management to find the root cause of the each and every waste
- Fill the “Tools” sheet in “Kaizen event Master file” with the root causes and send to Lean leader
- Visit for the role of the steering committee for lean
- Team selection, leader selection & their activities training/ meeting with steering committee/ making operator training calendar/ train the operator for lean/5s, etc.
- start operator training for multiskilling/make format for training/ 5s in Bangla/ Arrange training program for staffs for Needs for change/discuss with all PM for process standardization& sledding. Inform lean officer for next presentation/ training session with all line chief & floor managers
- Training program for Composition of SMV/ cross-training for operator/attachments for a machine.
- Training program for Types of waste/ wasteful motions/ cross-training for operator/attachments for machine/ searching machine
- Training program for practical waste full motion on the line/ Charles assessment review & findings.
- Conduct a meeting for the Economical & simultaneous motion/ Quality system of the line.
- Training program for Engineering sheet / Line chief & supervisor/ Martine visit the factory / Cross-training for the operator
- Training program for machine adjustment/ Training program for calculation KPI’s / Line chief & supervisor/ Martine visit the factory / Cross-training for the operator/ 4th training session for steering committee “How to Develop?”
- Report making / Marking & evaluation/ and visit the plant
- Team selection from finishing, leader selection & their activities training/ train the operator for lean/5s, etc.
- Start training session for team #A for just in time/ Understand 5s
- Training program for Composition of SMV & workplace development/different types of waste in the workplace & how to create continuous flow/ discuss with Mr. Aminul regarding QA procedure & arrange a meeting for continuous movement of the garments.
- Training about wasteful motion (theory & practical)
- Lean awareness training for finishing team A QC’s, Lean awareness training for team # 10 front & bk at (2 to 3 pm & assemble 3-4 pm).
- Economical & simultaneous Motion for the team leader, supervisor in finishing team #A, a Quality system of the line & product training for the team leaders & supervisors. Train the operator QA, the sup of team # 5 in two groups (front & bk 2to 3 & assemble 3-4 pm)
- Training about operation breakdown, critical path, quality & tool (work aids), worker balance, Layout & machine requirements.
- Training in finishing Btn area for 5s & lean concept & cross-training in team #A
You may also love to read
Implementation of Lean Manufacturing in Garments Factory