Sublimation printing is a digital printing technique, which uses heat to transfer dye into fabrics such as polyester and polymer-coated substrates. The printing process involves printing a design onto special transfer paper using sublimation ink. Using heat and pressure to transfer the ink onto the fabric. The sublimation printing is durable in nature that will not normally fade over time.
History of Sublimation Printing
Sublimation printing was first developed by a Swiss engineer named Sigmund Freudenberg in the early 1960s. According to his findings, using heat and pressure it is possible to transfer dye from a solid form into a gas and then back into a solid form again.
This process was later refined and commercialized and now it becoming widely used in the textile industry.
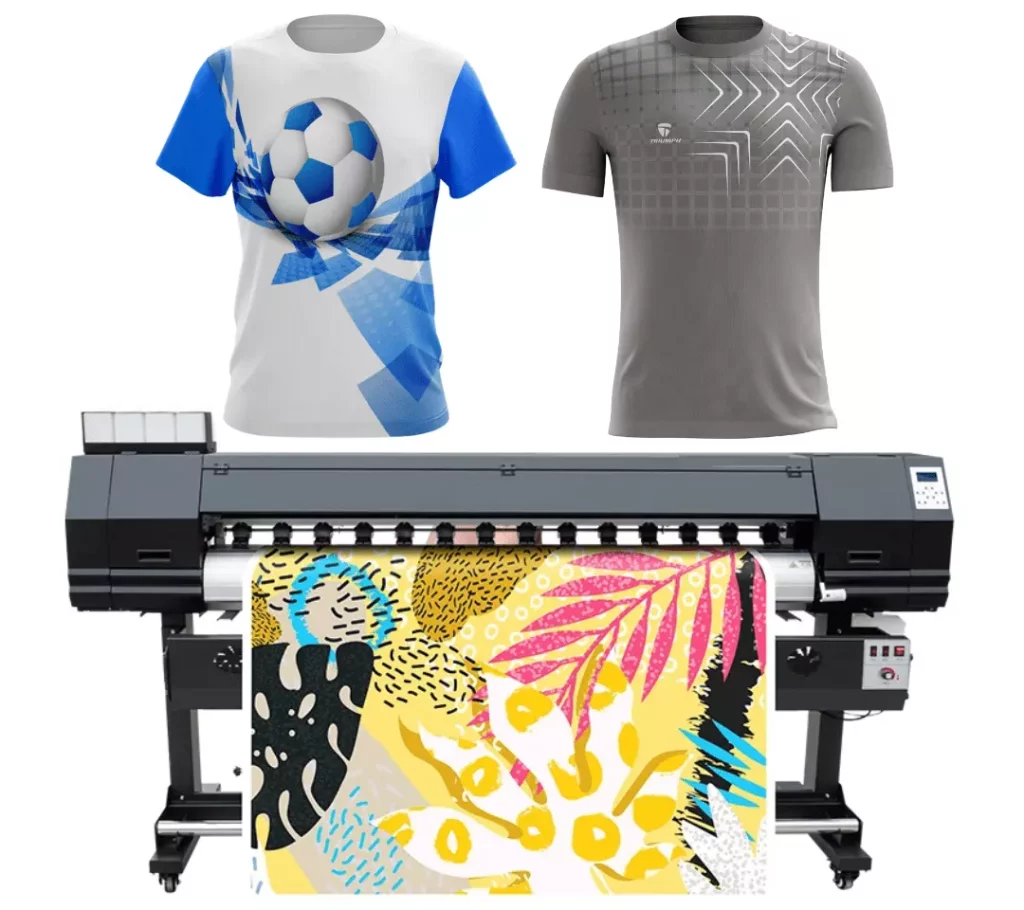
Applications of Sublimation Printing
Sublimation printing is widely used in the textile industry for a variety of applications such as:
Custom Apparel
This is often used to create custom apparel such as sports uniforms, t-shirts, and hoodies. The process allows for full-color, high-resolution prints that are durable and long-lasting printing.
Home textiles
To create custom bedding, curtains, and other home textiles. The process allows for the creation of unique and personalized designs that can be printed on a variety of fabrics.
Promotional products
To create custom promotional products such as bags, umbrellas, and keychains. The process allows for high-quality, full-color prints that can be used to promote a brand or event.
Technical textiles
Sublimation printing is also used in the production of technical textiles such as outdoor wear, protective clothing, and industrial fabrics.
Soft signage
To create custom banners, flags, and other types of soft signage this type of printing is used. The high-quality prints are suitable for indoor and outdoor use.
Sublimation printing is a versatile and cost-effective method for producing custom textiles and promotional products, which makes it a popular choice in the textile industry.
SOP of Sublimation Printing
The standard operating procedure (SOP) for sublimation printing on fabric typically includes the following steps:
Design Preparation
The design is created using specialized design software such as Adobe Illustrator or CorelDRAW. The image can be saved as a .jpeg or .tiff format. The file format depends on the printing machine’s preference.
Printing on Sublimation Transfer Paper
The design is printed onto sublimation transfer paper using a sublimation printer. Each printer is calibrated for optimal color and density. The transfer paper is loaded carefully into the printer according to the manufacturer’s instructions.
Heat Press Preparation
The heat press is set to the appropriate temperature and pressure for the fabric. The set temperature normally ranges between 380-410F (193-210C) and the pressure is around 40 psi. The time varies between 60-90 seconds, which is set according to the fabric type, and thickness.
Heat Pressing
The printed transfer paper is placed onto the fabric and then pressed using the heat press. The heat and pressure cause the ink on the paper to turn into a gas and bond with the fibers of the fabric. It is required to preheat the fabric to remove any moisture or wrinkles and align the design properly before placing it on the heat press.
Cooling
The purpose of cooling is to allow the dye to fully bond with the fibers of the fabric. The process typically involves removing the fabric from the heat press and allowing it to cool for a few minutes. The exact time will depend on the type of fabric, the thickness of the fabric, and the design that was printed. In general, thicker fabrics may require longer cooling times than thinner fabrics.
Remove Transfer Paper
Once the fabric has cooled the transfer paper can be removed. The fabric should be held steady and the transfer paper should be slowly and carefully pulled away from the fabric at a 180-degree angle. It is required to avoid pulling the paper in a different direction or at sharp angles to avoid any distortion on the print. Note that the transfer paper should be peeled off while the fabric is still warm, if the fabric cools down completely the transfer paper may stick to the fabric, making the peeling process more difficult.
Quality control
Once the transfer paper is removed, the printed fabric should be inspected for any defects or inaccuracies, such as color accuracy, density, and alignment.
Advantages of Sublimation Printing
Sublimation printing has several advantages over other printing methods; some of them are as follows:
High-quality, full-color prints
The printing allows for the creation of high-resolution, full-color prints that are vibrant in nature.
Durable and long-lasting
The sublimation ink is absorbed into the fibers of the material, making the print resistant to fading and cracking.
Versatile
Sublimation printing can be used on a wide range of materials, including polyester fabric, metal, ceramics, and more.
Cost-effective
This printing method is cost-effective for producing high-quality, custom textiles and promotional products.
No setup costs
Unlike screen printing, sublimation printing doesn’t require any setup costs, which makes it more affordable for short-run or one-off orders.
Flexibility in design
The printing allows for flexibility in design, you can print any design with any number of colors, patterns, and designs without any additional costs.
Environment friendly
Sublimation printing is a digital process, which means it does not use any chemical or physical processes, making it an environment-friendly process.
Cons of Sublimation Printing
While sublimation printing has many advantages, there are also some limitations and drawbacks to consider, some of them are:
Limited to specific materials
Sublimation printing is primarily limited to materials that contain polyester or have a polyester coating, it doesn’t work well on natural fabrics like cotton, rayon, or silk.
Color limitations
Sublimation ink is not as vibrant as pigment ink and there may be some limitations in the range of colors that can be achieved.
Quality control
Proper calibration is required and the maintenance of the printer and heat press, as well as correct ink and paper usage.
Heat press size limitations
The process requires a heat press to transfer the ink from the paper to the fabric, which can be limiting for larger or oddly shaped items.
Shrinkage
Some fabrics may shrink after the sublimation printing process, which can affect the final dimensions of the printed product.
Cost
The equipment and supplies can be expensive which makes it less suitable for low-volume projects.
Finishing
The process doesn’t provide a glossy finish, it’s important to consider a UV coating or lamination to achieve a glossy finish.
Conclusion
Sublimation printing is a digital printing method that uses heat to transfer dye into fabrics such as polyester and polymer-coated substrates. This method produces vibrant, high-quality designs that are highly durable and long-lasting.
However, it also has its limitations, such as being limited to specific substrates and requiring a higher initial cost for equipment and materials. Additionally, it requires specialized knowledge and skills to produce high-quality designs. Despite these cons, sublimation printing is a popular choice for a wide range of applications, including sportswear, home decor, promotional items, and customized gifts.
As the technology continues to evolve and improve, it is likely that even more applications will be developed for this versatile printing method.
Overall, sublimation printing offers a unique and effective way to create custom designs on a wide range of substrates, making it a valuable tool for businesses and individuals alike.