Dimensional Stability in Foil Print
How to Obtain Dimensional Stability in Foil Print While Keeping the Desired Shade Within an Optimal Process for Compact Jersey fabrics.
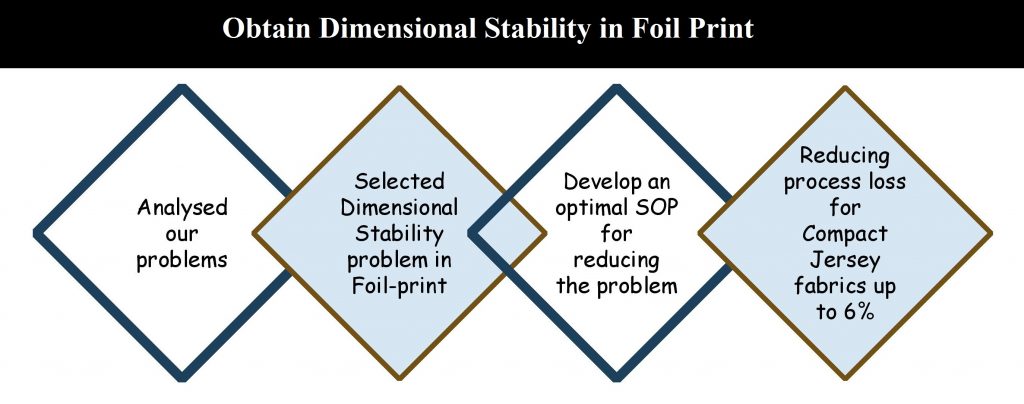
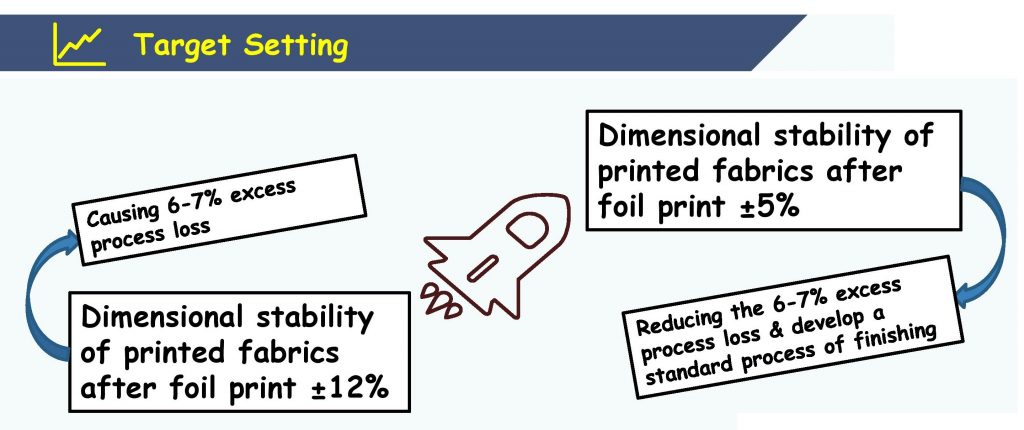
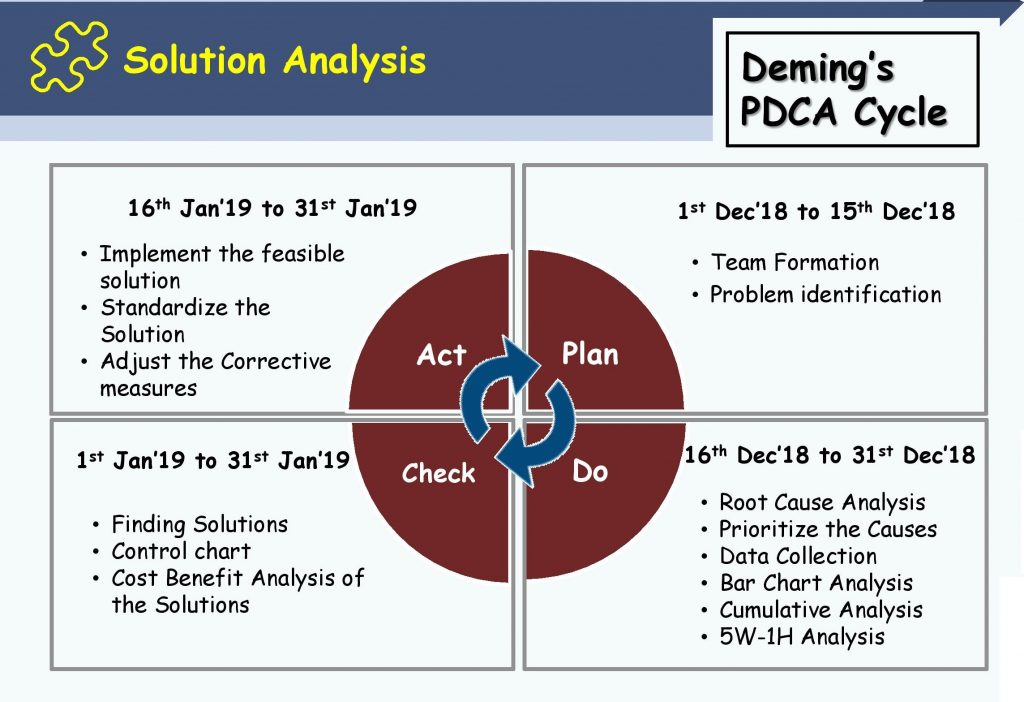
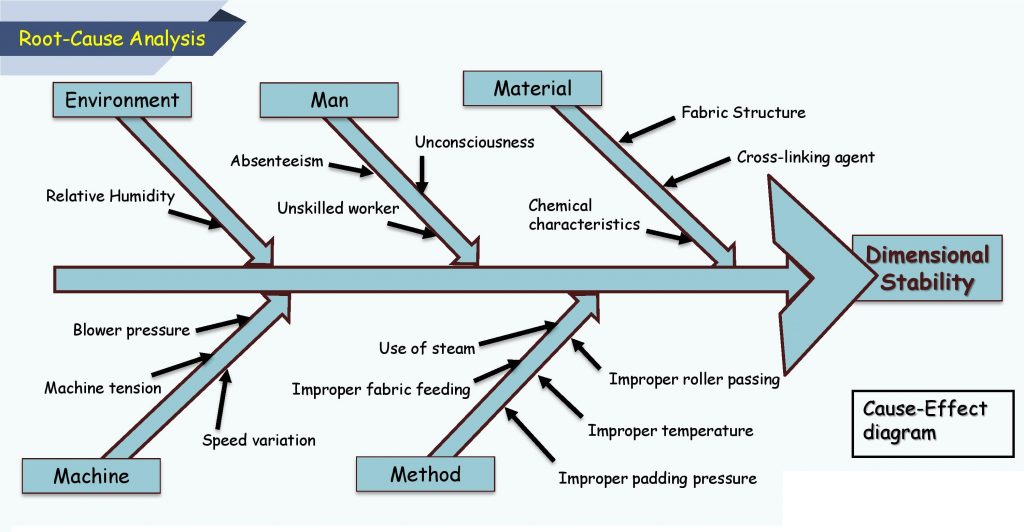
Solution Analysis
Problems | Resource R. | Feasibility | Significance | Time-Saving | Total | Priority |
Fabric Structure | 1 | 1 | 9 | 1 | 12 | 8th |
Chemical characteristics | 2 | 2 | 8 | 2 | 14 | 6th (2) |
Cross-linking agent | 2 | 2 | 8 | 2 | 14 | 6th (1) |
Improper roller passing | 5 | 5 | 7 | 2 | 19 | 4th |
Improper temperature | 8 | 8 | 9 | 3 | 28 | 1st |
Improper padding pressure | 7 | 8 | 9 | 3 | 27 | 2nd |
Relative Humidity | 2 | 3 | 6 | 1 | 12 | 8th |
Absenteeism | 3 | 5 | 4 | 1 | 13 | 7th (1) |
Unskilled worker | 2 | 2 | 6 | 3 | 13 | 7th (2) |
Blower pressure | 2 | 3 | 4 | 1 | 10 | 9th |
Machine tension | 1 | 1 | 5 | 2 | 9 | 10th |
Use of steam | 4 | 3 | 8 | 1 | 16 | 5th |
Speed variation | 5 | 5 | 9 | 4 | 24 | 3rd (2) |
Improper fabric feeding | 7 | 7 | 9 | 1 | 24 | 3rd (1) |
Unconsciousness | 7 | 1 | 3 | 1 | 12 | 8th (3) |
5W-1H Analysis (Reason 1)
Question | Improper Temperature |
Where does it happen? | In Finishing |
Why it is a problem? | Affects foil shade |
What to do? | Find out an optimal temperature |
Who will do? | QCC team |
When will do? | Within 1 month |
How much it will cost? | Moderate cost |
Developing Solutions for Reason 1: Improper Temperature
S/L | Solution suggested | Analysis | Remarks |
1 | a) Dryer + Compacting above 100ºC b) Stenter above 100ºC | Shade not ok | Not accepted |
2 | Dryer below 100ºC | Shade ok, but dimension fails in lengthwise & diameter short | Not accepted |
3 | Compacting | Shade not ok | Not accepted |
4 | Stenter below 100ºC | a) Shade ok but dimension varies with pressure b) Shade & dimension ok; but, requires 5-6% excess process loss due to GSM problem | Need more analysis |
5 | Tumble Dry | Shade & dimension ok; but, requires 5-6% excess process loss due to GSM problem | Need more analysis |
5W-1H Analysis (Reason 2)
Question | Improper padding pressure |
Where is happens? | In Stenter machine |
Why it is a problem? | Affects foil |
What to do? | Find out an optimal pressure & avoid maximum pressure |
Who will do? | QCC team |
When will do? | Within 1 month |
How much it will cost? | Moderate cost |
Developing Solutions for Reason 2: Improper Padding Pressure
Solution suggested | Analysis | Remarks |
Stenter below 100ºC with double padder | Affects foil for high pressure & causes lengthwise extension resulting dimension failure | Not accepted |
Stenter below 100ºC with single padder (maintaining low pressure) | Shade & dimension ok | Accepted |
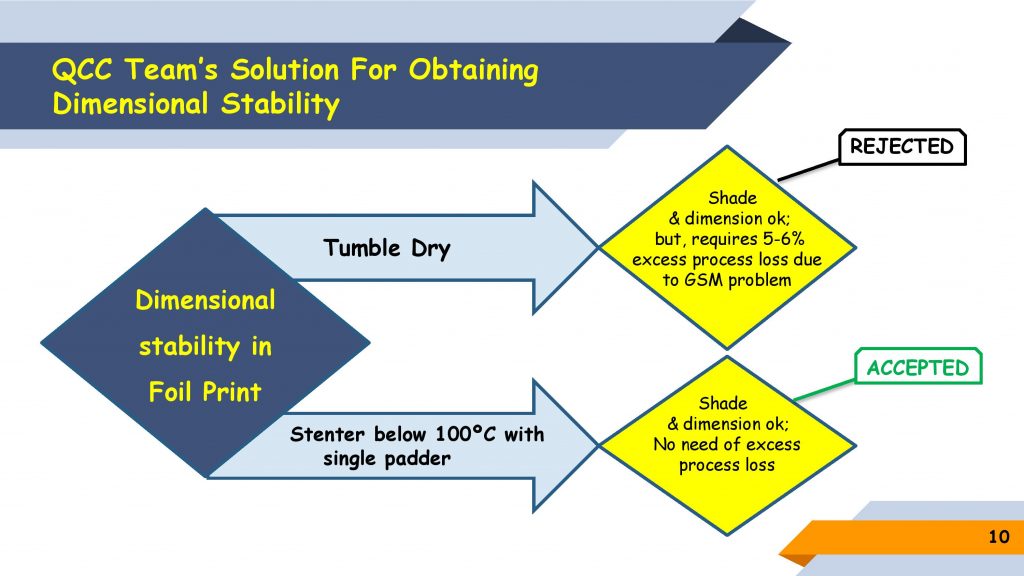
Foreseeing Resistance
Resistance | Analysis & Solution |
Dimensional stability is changed after foil print due to Delamination | Control GSM, Shrinkage & Water Absorbency before printing (semi-finished while gumming & cutting) |
If finished before printing, absorbency may be reduced at finishing | Used Hydrophilic Softener |
This technique is not applicable to loose knitted fabrics | We will work on this in our next project |
Result Analysis
Order Number: GISGM1419
Fabrication: 100% Cotton, Interlock, Diameter- 62’’, GSM-180
Order Volume: 3,130 KG
Fabric Delivered: 2912 KG
S/L | Parameter (after finishing) | Tumble-dry | New Process |
1 | Processed quantity | 1490 kg | 1422 kg |
2 | Diameter | 57~59’’ | 60~62’’ |
3 | GSM | 188~192 | 175~182 |
4 | Consumption | 6.8% more | No excess required |
The final result achieved from our project
Dimensional Stability | Buyer requirement |
Fabric save | 0.068 |
Foil Save | 0.074 |
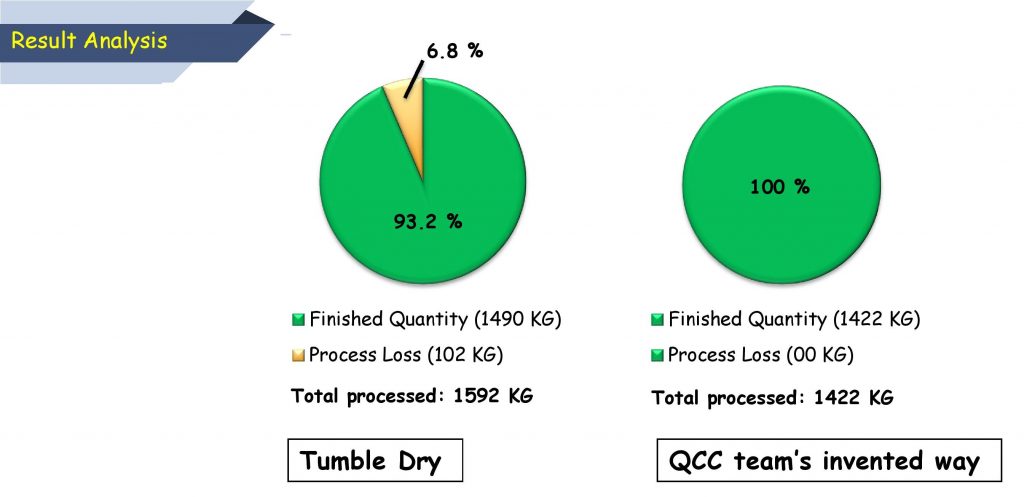
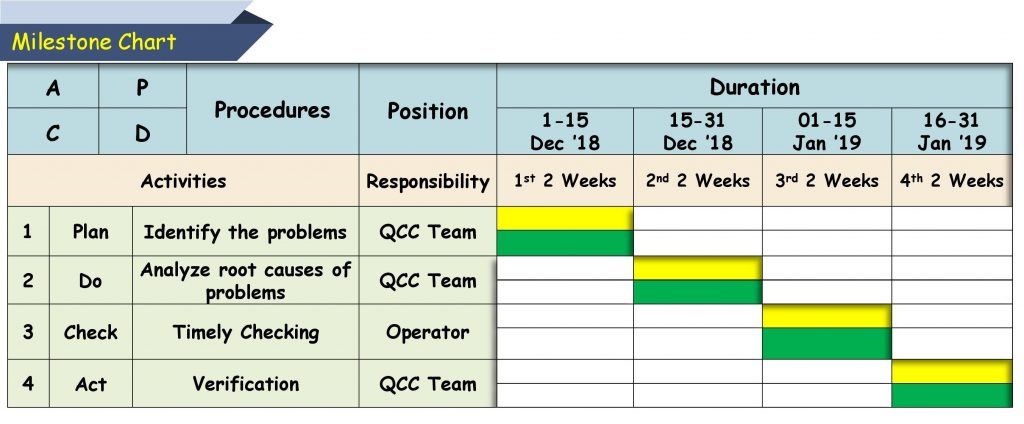
Written By
Sharmin Akther Diba
Industrial & Production Engineer
Email: [email protected]
How to Obtain Dimensional Stability in Foil Print