The best practice is a manufacturing methodology or technique which is developed by longtime research and accepted as the best method to do a particular job. Here I am giving best practice followed by Garments washing factory, you may set them as a standard operating procedure (SOP) for the whole washing process. Hope this article would help you enrich your knowledge of best practices of Garments Washing Factory.
Best Practice of Garments Washing Factory in Apparel Industry
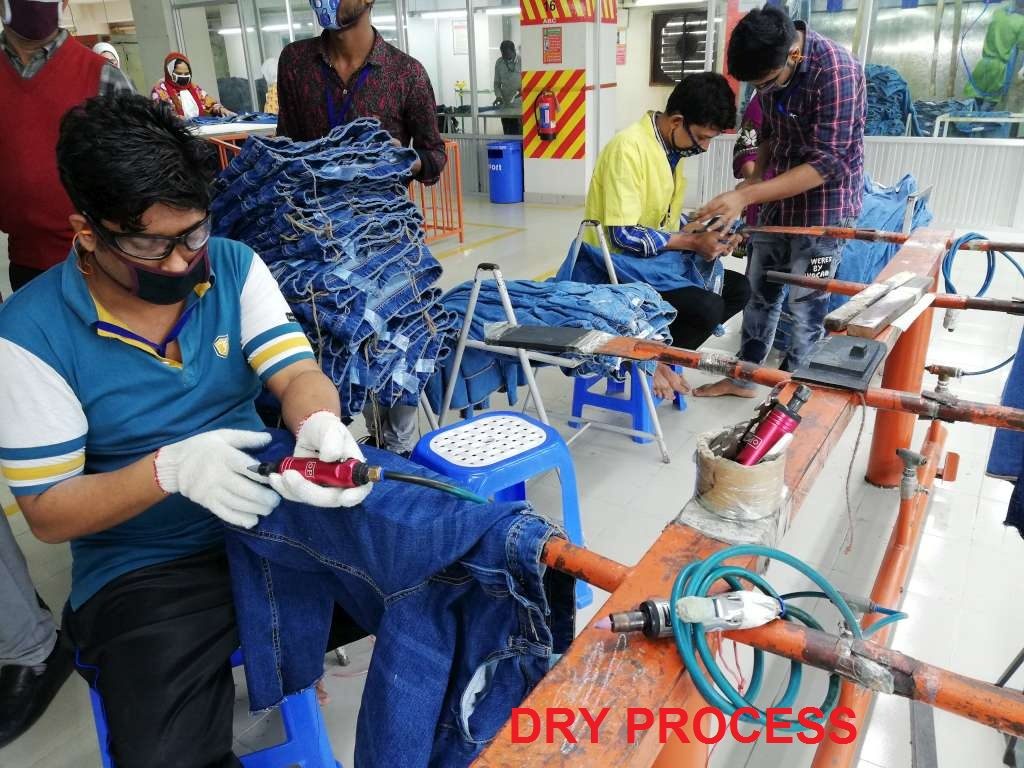
Pre-Production /Sample Development Stage of Garments Washing Factory
- Set a detailed SOP for sample development and pre-production procedure and team organogram for proceedings, make visible for all.
- Your factory should have a separate department or a team (R&D) for handling samples development and duplication.
- Development samples, and then duplicated samples are kept with records/recipe for future follow up.
- Development team reviews the PDM & check requirements before start shade band/the first batch.
- Developments samples are scan and reviewed by supervisor/manager before submitting for approval to buying-house.
- Trims and Leather patches being reviewed/Wash standard Checked prior to development.
- Risk Analysis meeting is to be held in factory or vendor to take necessary precautions before bulk & maintain the records.
- Washing recipes are set with record according to approved samples/standards/recipe/work order.
- Samples are reviewed under lightbox in dark room with identified light sources from an individual customer for color matching.
- Shade blankets/Shrinkage test done properly as per Wash standard.
- Always run a 1st batch trial and review it in detail, for measurements, appearance & shade, before running bulk production. Make a detailed report.
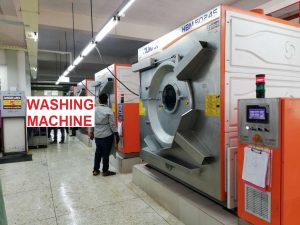
Production Control -Dry and Wet process in Garments Washing Factory
- Inspecting Garments in before the wash stage to check part shading, work hole, spot, and shade segregation.
- Approved samples for each dry process available (with date & signature) and posted in front of the operator.
- Inspection procedure by AQL check for defects, keeping a daily updated report of pcs checked & defects found, use min 1,000 lux illumination, proper records kept before proceeding to the next process.
- Quality Improvement efforts with Quality meetings, Defects Summaries, Pareto Analysis and Follow up. Use statistical data, to analyze quality results & make decisions to improve it. Review results & plan future corrective actions based on root cause analysis (should be visible in production lines), Pareto graph, and follow up on top 5 defects. Compare results by day, week, month and by-line, section, dept., etc. You need to also keep track of the progress of at least 1 most recurring defect
- The first bulk lot procedure is available in the wash plant with a color-coding system.
- Garments are properly prepared and weighed/load size accordingly to suit machine sizes and work orders prepared.
- Approved recipes are properly prepared and posted for operators guide on each particular finish/machine.
- Garments are checked for scratch, color-matched to standard before applying the next step of the wash/soften bath.
- You should have an in-house lab testing room, important Lab testing carried out at internal Lab e.g.: pH /tearing/washing fastness/crocking, etc.
- Washing standards and shade bands available for each style/color and stored properly by dark ploy in a locked box.
- Measurements checked on every batch before and after washing, using a correct ruler, and calibrated tape measurement and reported.
- The implementation of the Preventive Maintenance system to reduce machine downtime and maximize machine fitness.
- Color evaluation Lab is maintained with buying house standard light source, CWF & D65 preferable.
- Implement 5’s method as a base to implement lean procedures. Must do weekly 5’s audits, give & post rating to each area. Do formal training & keep training records.
- Set up ETP and WTP to remove effluent from water and processing wastewater.
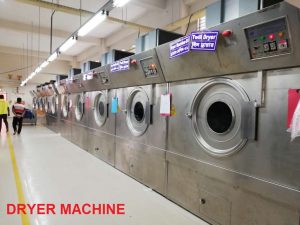
Chemicals/ Dyestuff Control and Storage in Garments Factory
- Set a detailed SOP on chemical storage, dispatching, and chemical handling safety procedure to visualize on the floor.
- Temperature and humidity control, Storage area ventilation, and floor set in good condition.
- All containers, big & small must be properly labeled to indicate which chemical they contain.
- Chemicals arrangement in good condition to avoid accidental/hazardous/inflammable mixing.
- Keep a log of chemicals dispatched to bulk production, quantity & chemicals specs must match the washing recipe.
- RSL, MRSL reports must be handily available on site for each chemical. GOTS certificate, MSD, and TDS documents should have in chemical and Dyestuff store.
- Warnings signs are posted on shelf or wall for, especially chemicals in storage.
- Dispensers are properly labeled for separate applications to avoid chemicals Contamination.
- Weight machine or digital balance in use, Scales must be calibrated for accuracy.
- Chemicals are well prepared and weighted in advance for bulk production load.
- Stockkeeper in control of chemicals used.
- Chemicals are labeled to containers/bags of purchase date or expiry date.
Technical requirement of cutting and Fabrics
- Garments dry process and wet process procedures
- Garments washing procedure
- Garments washing best practice
- Benchmarking Garments washing.
- Technical Requirement of Cutting and Fabrics
Best Practice of Garments Washing Factory