5S comes from 5 Japanese words and each of them starts with S. These are seiri, seiton, seiso, seiketsu, and shitsuke, if we translate these 5 Japanese words into English then we get Sort, Set in Order, Shine, Standardize, and Sustain. In the garment industry 5S works as a basic tool of Lean Manufacturing, a technique to set a well organized, clean, and visually attractive workplace. That’s why the implementation of 5S in the Apparel Industry is required.
Implementing the 5’S method is a base to implement quality improvement/lean procedures. Expecting the team to be and they do activities in each department: like monitoring, evaluate and drive the aspects very clean and organized so that, your Factory will look very planned and well Set-up.
Let’s have a look at the difference in English and Japanese words for 5S
Basic Concepts for 5S Implementation in Apparel
S1. Sort (Seiri)
5S start with sort. Sort means to sort out unnecessary items, use all machines, tools, equipment for regular use. Define daily needed items, weekly needed items, and monthly needed items and keeping separate. The store is broken, unusable or occasionally used items also should be defined. Keep records for eliminating unnecessary items that exist and new items. Each and every section of garments you may find many things are kept in a haphazard way. So for these, you need to follow the first S from the 5S, i.e Sort. Sorting according to items characteristics and importance.
S2 – Set in Order – SEITON
Setting order is important for 5S. All items, sections, and areas (In, exist) are clearly identified by a label and everything should be well organized. Never mix/store two category items in one place. Dividing lines, aisle mark, Stairway is clearly identified and clean as per standard. Confirm that the exits are accessible and unlocked during working hours. Confirm that, where necessary, the emergency exit doors have no panic hardware or lever style (one hand, one motion door openers). If you keep all of your store materials in your garments warehouse in a planned order basis, then whenever required that materials you can easily find out and get those materials. That’s why all materials should be kept in accordance with the set in order.
S3 – Shining – SEISO
The third S from 5S is Shine, actually mean cleanliness. All items/place of workplace Floors, walls, stairs, ceilings, pipework Racks, cabinets, shelves, Machines, equipment, tools, Stored items, materials, products, and lighting everything required to be kept clean. All cleaning tools and materials are easily accessible. Cleaning assignments are defined and are being followed by the checklist and hang checklist on visible board. Do periodical pest control to make sure there is no insect. Cleanliness is not only a compliance issue but also this increase a healthy working environment in garments factories or offices.
Download: S3: Shine, Cleaning Schedule (Excel 20kb)
S4 – Standardize – SEIKETSU
The first three steps of 5S are the key to implement 5S in the workplace. This section is about visualization by Information displays, related SOPs, signs, color coding and other markings are established everywhere of the factory also included procedures for maintaining the first three S’s are being displayed. Do regular 5’s audit using a checklist, give & post rating to each area. Need formal training, keep training records to approach towards improvement. These standardizations increase the operating efficiency of the apparel industry.
S5 – Sustain – SHITSUKE
This section is to sustain 5S in the textile and garments factory to be the way of life rather than just a routine. Success stories are being displayed (i.e. before and after pictures) in every section of the 5S board. Give rewards and recognition is part of the 5S system to sustain 5S.
S6 and S7(Extension of 5S)
Now, 5S have two additional points 6th “S” for “Safety” and the 7th “S’’ is “Security”. These two new points’ objective is to make a safe workplace for all employees. It is the employer’s responsibility to provide safety and security for both factory and office place in the apparel industry.
Advantages of 5S for Garments
If you properly follow 5S for your textile and garments industry, then you will get the following benefits:
- Health and Safety is ensured
- The base of implementation of quality improvement
- Productivity Increase
- Save time, cost and storage space
- Minimization of accidents & mistakes
- Increases efficiency
- Creates workplace ownership
- The first step for Lean procedures
- Increase customer satisfaction
- Reduce inventory time
- Reduce downtime, wastage
- Good working environment
- Visualization and labeling
- Boost morale
- Improve company image
- Optimize organization and workplace as per requirement
- Routine wise work schedule and visual Standard Operating Procedure (SOP) everywhere
- Everybody knows their working responsibility where and when
- Disciplined housekeeping
Implementation of 5S in Apparel Industry
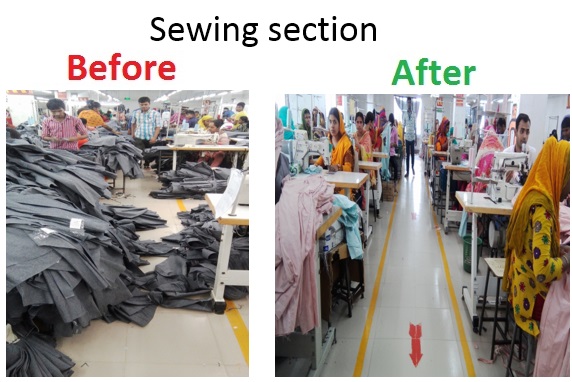
For implementing 5S in Apparel Industry you need to follow the followings:
- Need central 5S committee and section-wise subcommittee
- 5S organogram and committee list as enclosed
- Section-wise 5S checklist
- 5S display board in every section
- Make a separate T-shirt for a committee
- Conduct 5s training and drive for good housekeeping
- Conduct a section-wise 5S audit and submit a report.
- Evaluate score and take corrective action for improvement in every department.
Actions Need to Implement 5S in Garments Industry
- Take “before” photographs.
- Check that the first three S’s are implemented properly.
- All team activity documents/checklists should be publicly displayed on a 5S board.
- Establish the routines and standard practices for regularly and systematically repeating the first three S’s.
- Standardize red tag procedures and holding area rules (see Seiri).
- Create a maintenance system for housekeeping. Make a schedule for cleaning the workplace. A common approach is to ask a cross-functional team to do it.
- Inter-departmental competition is an effective means of sustaining and enhancing interest in 5S.
- Assign responsibility to individuals for a work area and machinery.
- Regular inspection/audit and evaluation by a special team (including senior management persons) to be continued.
- Instead of criticizing poor cases, praise and commend good practices or good performers.
- Take “after” photographs and post them on the 5S board(s).
- Give a reward for the top-scoring section.
You can download Presentation File on 5S if you need it.
5S Presentation: PowerPoint (6.3MB)
5S Training: PowerPoint (5.1MB)
5S Presentation (English & Bangla): PowerPoint (6.9MB)
MaasyaAllah, thank you very much Pak Washim for sharing this knowledge. It helps me a lot.
Jazakallahu khoiron.
Barakallahu fik.
5S is an integral facet of manufacturing excellence. Though early resistance may be felt, the benefits will soon become apparent. Visual Management is absolutely key. Great article.
Thanks a lot for your idea sharing with us. It is great post!
It’s a great idea for me thanks for published it .
Good
Thanks for sharing your info.
I was able to find good information from your blog post