‘Layout’ is simply the orientation of product or process flow. From our day to day life it has so many significant impacts. In the RMG sector, every section has a specific kind of layout system as per work standard. Garments finishing is the last stage among the top three stages (Cutting>Sewing>Finishing). Whether it is knit, denim, woven, sweater, or lingerie, the finishing unit has some style of line layout as per company or space or product. This is called the conventional way of Finishing layout, which is widely used. But this conventional system reduces finishing efficiency. As finishing efficiency has a direct impact on CMT cost (Cut, Make & Trim), now it’s time to reshape our layout from conventional to ‘Rail-line layout’ system. This article will be discussed about the rail-line layout system, how to implement it & its advantages for garments finishing unit. Though we are going to discuss the finishing layout system, you can implement this kind of layout system on your sewing floor also.
What is Conventional Layout System and Rail-Line Layout System?
The conventional layout system is the layout system that we mostly use on our finishing floor. We have fixed finishing lines of fixed length & width with aisles among them. We put Trimmer (Manual or auto), specification checker, visual checker, iron man, keep operator for trims & accessories adding, Final checkup, folding (Manual or auto), wrapping & packing, etc.
On the contrary, the rail-line layout system contains all the processes from above, the same manpower, the same space, just need a rail line system with hanger. This rail-line may be a hollow steel or plastic pipe hanging up a little bit arch where hanger can be moved easily. Or it may be a moving conveyor with hanging garments attachment. A Conveyor system is used for the sewing line mainly.
Conventional Layout Vs Rail Line Layout System of Garments Finishing Unit
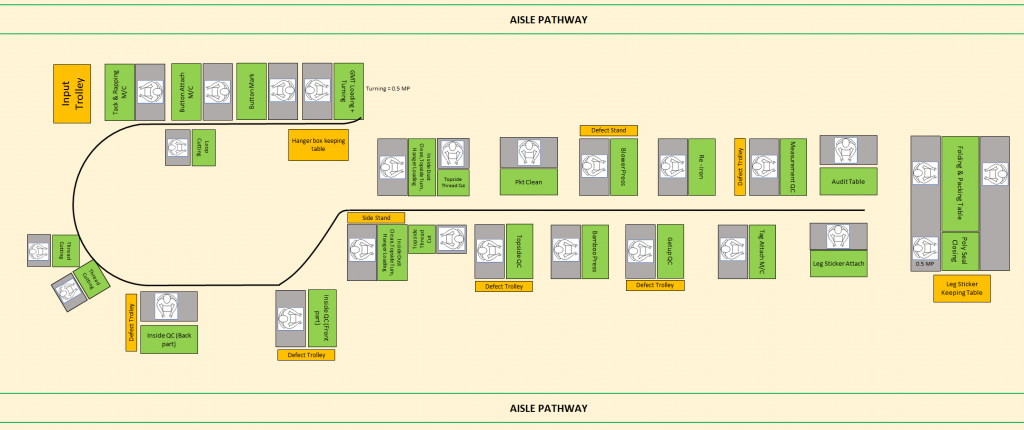
Structure of Rail Line Layout System
- The layout starts at the point of the hanger box keeping table, yellow marked. On the same side, there is an input rack or trolley. From there Garments loader will bring & hang garments in the hanger to start the flow. You can see turning we mention 0.5 manpower. That means if you make the rail-line layout system in your floor such a way that two parallel lines share side by side input point; then one person can be used for two lines for garments turning. We keep this turning in the finishing line to do manpower optimization. But in a conventional way, we use turning helper in sewing & most of the cases use one person.
- Another best use of this layout is adding accessories in the finishing line. Here button attaches shown in the finishing line. In this way, hook & bar, buckle, snap button can be attached in finishing to avoid destruction or breakage while transportation or washing. Garments loader will flow the hanger to the assistant operator for button positioning (It may be avoided as per garments type or requirement); after that button attach operator will do his/her work while keeping the garments in a hanger. Then the next operation of loop cutting followed by tack & wrapping operation of care label, as per product requirement.
- Followed by tread trimming operation, there was some space for garments hanging as input for thread trimmer helper. Then comes inside quality check. It may be subdivided into the front or back part or left or right side inside QC. There will be defective trolley keeping them segregated with different types of defective products. This type of layout system strongly avoids a backward flow. It needs to keep defective products stored, after a fixed time interval it will be collected & fixed by line supervisor, QC supervisor, or line manager with necessary remedies.
- If it needs dust cleaning then full garments will be open from the hanger, clean, turn & hang it to the line. In this section, the side stand can be kept to keep defective garments if found. Then pass it through rail-line to topside thread trimmer. The number of topside thread trimmer is less than inside thread trimmer. After that workstation of topside thread trimmer with defect stand or trolley. After that garments pocket cleaning.
- It comes ironing operation now. There will be waist side press, side press, crease press, etc. as per product requirements. It is better to keep one or two defects stand. There will be an iron quality checker with segregated defect rack or trolley followed by measurement QC.
- It’s time to add necessary trims, stickers, etc. as per requirements. After that audit table to check the final product.
- Then comes folding, wrapping, or packing table as per product requirements. In this section, manpower can be shared with another line. By following this layout system, there will be much open space to keep line-wise finishing rack, trims & accessories keeping rack, etc.
Follow ‘Visual Management: A tool of Lean Management for Finishing Unit’ article for more information
Advantages of Rail-Line Layout of Garments Finishing Unit
- Optimal manpower
- Disciplined workplace
- No crease in garments
- Proper utilization of space
- No dust from excessive hand touch
- Lean Management in Finishing line
Limitations of Rail-Line Layout of Garments Finishing Unit
- Cannot be useful for short length product like tank top or lingerie
- Improper line layout may cause improper process management
- Bad quality hanger or mishandling can cause defective products
We need improvement in every section of the garments unit. For achieving this, it is necessary to start now with slow but continuous improvement. Though there are some limitations to this layout system, why not try a proto-type of one line in your finishing unit? With proper plan & set-up system, it is easy to implement. In the long run, you will get advantages. There are so many renowned buyers who want this kind of layout system for the sewing & finishing unit. For example, Walmart, Levis, Hagger, etc. buyer have some pre-condition before order placement to have this kind of layout system for their quality products. Hopefully, very soon we will adopt this layout orientation for our sewing & finishing product not only for a quality products but also for following lean management.
Written by
Sharmin Akther Diba
Industrial & Production Engineer
Rajshahi University of Engineering & Technology
Email: [email protected]
LinkedIn: Sharmin Akther Diba
layout is quite invisible, cant identify the flow, pls sent some big clear pic
please download the image and zoom in